Commitment.01In-house production for “working responsibly”
At SunMax’s Hokuriku Plant, “Design and Development Team” and “Production Team” work day in and day out to improve their technical capabilities. They design mechanical and electrical equipment by utilizing the information obtained from hearings with customers by sales representatives.
Based on this, the operations of processing, manufacturing, purchasing, and assembling each part are in-house production at the plant, which leads to “stable quality.” This is our system for “working responsibly” for all customers who use SunMax products.
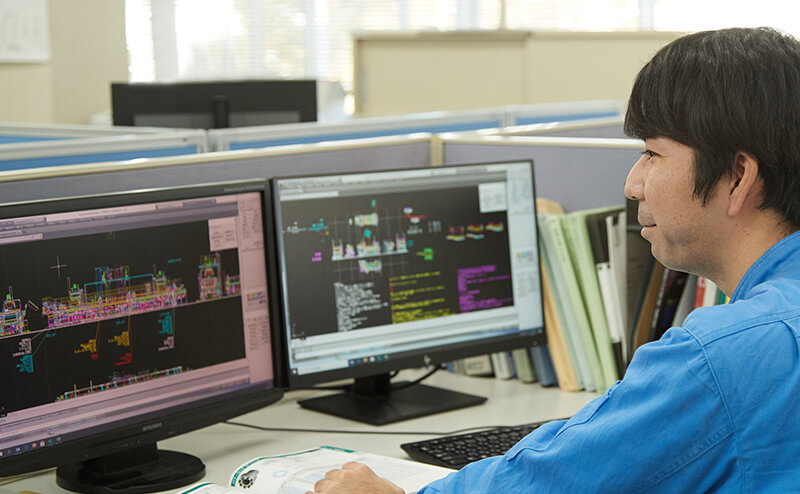

Commitment.02Design and Development Team: Embracing technical challenges
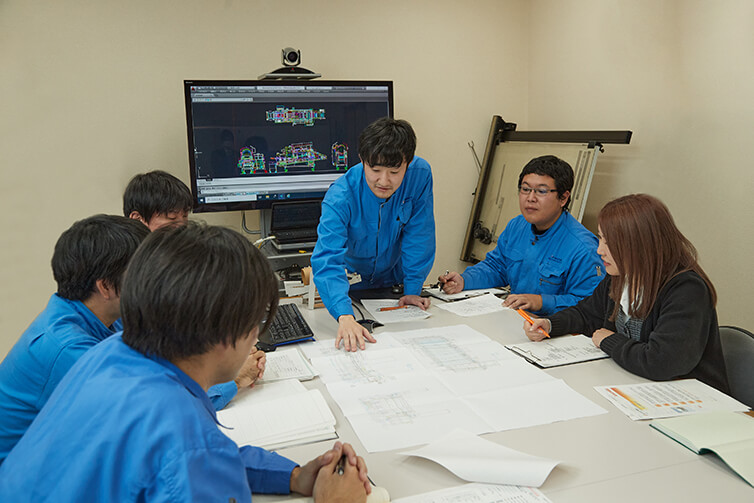
The fabrication process starts with a review of the product concept. The team reviews the product’s purpose and application and creates design drawings. Sometimes they fabricate a prototype and repeatedly evaluate its structure and safety before applying their findings to the design. In electrical design process, considering customer’s usability, they design hardware components in the control panel and software such as programming. The team also creates approval drawings, including outline drawings and customer requirements, as well as documentation (operation procedures, part lists, etc.) for submission to the customer. We pride ourselves on creating drawings and documentation that are easy for customers to understand.
At our Lab and Testing Room, the Design and Development Team plays the lead role in installing machines to prepare for the tests, conducting those tests in the customer’s presence, and cleaning the machines after the tests. We also take responsibility for these tasks, which are prone to be taken for granted. This approach is the most important element that backs up our technical capabilities.
Commitment.03SunMax quality: Found in every aspect of each machine and in our fine-grained service
Our goal is that customers will find SunMax’s dedication to excellence and quality in every aspect of our food processing machines. For example, necessary parts are fabricated entirely in-house, including laser cutting of frame materials, deburring, bending work, welding, lathe machining, milling, and drilling. Machines are assembled from finished sheet metal, processed parts, and purchased parts. Then they undergo a completion inspection. The Hokuriku Plant carries out a variety of inspections to verify that each machine is free of defects and that it has been built to specifications. Once the customer has seen the machine (after the inspections but before shipment), we make corrections and changes as necessary. SunMax quality means we then handle everything ourselves, including delivery of the machine, installation, test production at the customer’s facility, machine problems, and modifications.
Commitment.04Acting as a partner to help customers embrace the challenges of food manufacturing
Our sales team works with existing customers that are already using SunMax machines as well as new customers with inquiries. The team meets with the customer to determine specifications by considering factors such as the type of machine needed, available space, and production volume and then makes a proposal. Tests are carried out at the Hokuriku Plant’s Lab and Testing Room as necessary. We also deliver finished machines, conduct commissionings to verify proper operation, and provide maintenance and after-sales follow-up (repairs and service to address abrupt failures and other issues). Additionally, we visit the customer’s plant on a regular basis after delivery to inspect the machines. Our relationship with each customer does not end with the sale of the machine. Our goal is to provide robust after-sales follow-up, for example through repairs and inspections, and to serve as a partner to help customers embrace the challenges of food manufacturing.
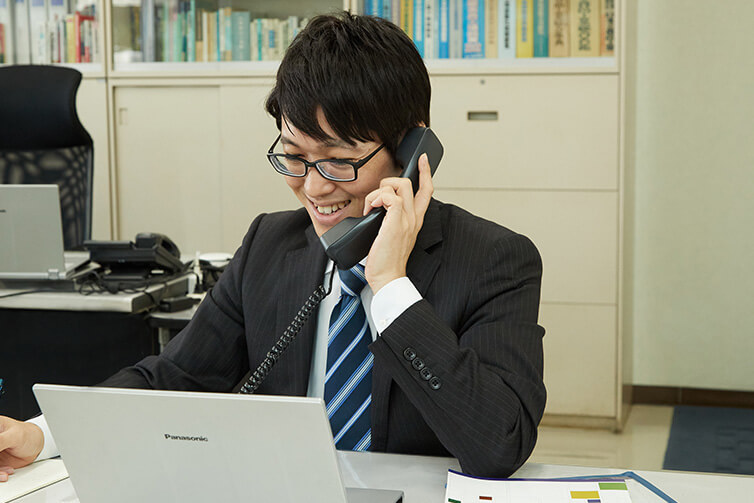